Primele piese imprimate 3D ajung în motoarele avioanelor Boeing
0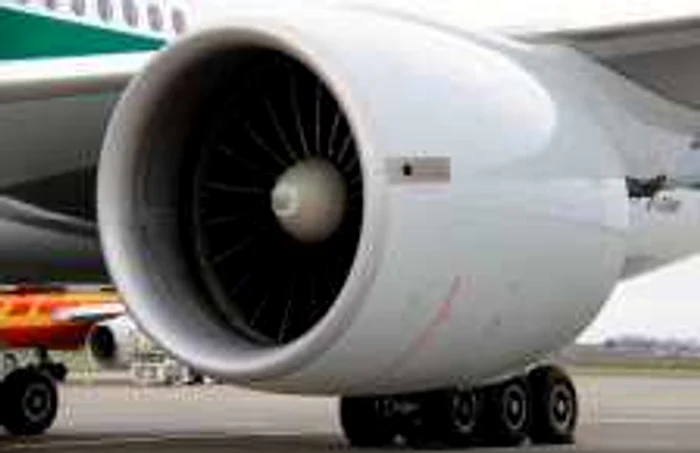
Prima piesă imprimată 3D, folosită la motoarele cu reacţie GE, a fost certificată de Administraţia Federală a Aviaţiei din State Unite (FAA), fapt ce marchează una dintre cele mai mari schimbări din domeniul aviaticii.
GE Aviation colaborează cu Boeing pentru a dota peste 400 de motoare cu reacţie GE90-94B - unele dintre cele mai mari şi mai puternice motoare din lume - cu piesa imprimată 3D
Carcasa din metal argintiu, de mărimea unui pumn, care adăposteşte senzorul de temperatură pentru duza compresorului unui motor cu reacţie este o piesă destul de puţin cunoscută, chiar şi de cei care sunt pasionaţi de aviatică.
În prezent, GE Aviation colaborează cu Boeing pentru a dota peste 400 de motoare cu reacţie GE90-94B - unele dintre cele mai mari şi mai puternice motoare din lume - cu piesa imprimată 3D. Familia de motoare GE90 pune în mişcare avioanele Boeing 777.
Viitoarele motoare vor avea mai multe piese imprimate 3D
Însă carcasa imprimată 3D nu va rămâne singură pentru mult timp. GE a început deja testele de zbor cu următoarea generaţie de motoare cu reacţie LEAP, dotate cu 19 duze de alimentare imprimate 3D. Motorul, care va fi folosit la noile aeronave cu fuzelaj îngust de tipul Boeing 737MAX şi Airbus A320neo, a fost creat de CFM International, o companie mixtă, la care contribuie în mod egal GE Aviation şi compania Safran (Snecma) din Franţa.
În plus, GE produce duze de alimentare şi alte componente imprimate 3D pentru motorul GE9X cu care este echipat noul avion Boeing 777X. Motorul GE9X va fi cel mai mare motor construit vreodată.
Oamenii de ştiinţa GE au început să testeze imprimarea 3D a diferitelor componente şi alte metode de "fabricare tridimensională" cu zece ani în urmă. Compania a efectuat o serie de tranzacţii cheie în domeniu, cum ar fi achiziţionarea companiei Morris Technologies, fondată de un pionier al imprimării tridimensionale, Greg Morris.
Avantajele imprimării 3D
Spre deosebire de metodele de fabricare tradiţionale, unde piesele sunt decupate sau tăiate dintr-o bucata mai mare de metal, fabricarea tridimensională "creează" piesele direct dintr-un fişier CAD, utilizând straturi de pudră fină de metal care fuzionează sub acţiunea fasciculului de electroni sau a razei laser. Această metodă permite crearea de piese complexe, care ar fi extrem de dificil sau chiar imposibil de obţinut printr-un alt procedeu. Timpul necesar pentru producerea pieselor prin această metodă este extrem de scurt si, în comparaţie cu metodele tradiţionale de prelucrare şi sudare, se generează un volum redus de deşeuri.
Astfel, cu ajutorul fabricării tridimensionale, inginerii pot înlocui angrenaje complexe cu o singură piesă, care este mai uşoară decât versiunile anterioare, reducând greutatea totală a motoarelor cu reacţie, ceea ce le face mai eficiente din punct de vedere al consumului de combustibil.
Noua carcasă imprimată 3D, fabricată dintr-un aliaj de cobalt şi crom, protejează circuitele electronice sensibile ale senzorului de temperatură de îngheţ şi de acţiunea dură a fluxurilor de aer din interiorul motorului.
"Imprimanta 3D ne-a permis o testare rapidă a piesei, a facilitat găsirea celui mai bun design şi lansarea rapidă a procesului de producţie", declară Bill Millhaem, manager general pentru programele de motoare GE90 şi GE9X ale GE Aviation. “În octombrie anul trecut am ajuns la forma finală a piesei, am început producţia, am obţinut certificarea FAA în februarie şi săptămâna viitoare piesa se va regăsi deja în interiorul motoarelor. În mod normal, carcasele sunt fabricate cu ajutorul unor matriţe, procedură care nu ne-ar fi permis niciodată să ajungem atât de departe."